Mig Welding Tips and Tricks Welding Guide
MIG WELDING BASICS
Mig Welding Tips
- Direct your wire at the leading edge of your weld pool for the most control of your weld bead.
- For the most bead control when doing more difficult welds such as; Vertical, horizontal, and overhead welds, use the smallest wire diameter possible, and keep you weld pool small.
- Your contact tube, gun liner, and drive rolls should coincide with your wire.
- Keep your gun liner, drive rolls, and gun nozzles clean. Contact tips should be replaced if there is blockage, or not feeding the way it should.
- Your gun should stay straight, ensuring the wire will feed properly.
- Steady the gun with both hands.
- Do not over tighten wire feeder hub tension and drive roll pressure.
- Store your wire in a place that is contaminant free.
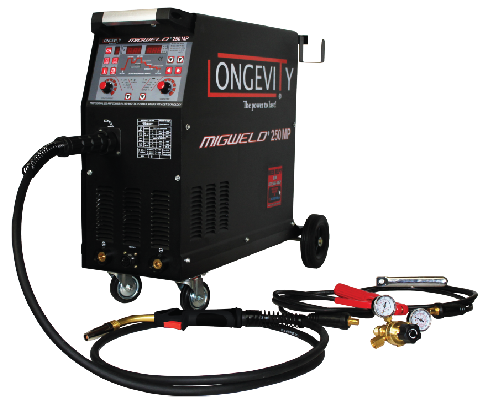
Electrode Tip

Electrode Length
Never let your electrode’s distance from your contact tube exceed 1/4” to 3/4” . If you do your weld will not be correct.
Too Short | Normal | Two Long |
![]() |
![]() |
![]() |
WELDING WIRE
Welding Wire Length
Thin Metal=Thin Diameter
Thick Metal= larger wire, with a larger machine
Use the wire that matches your metal. Don’t use aluminum with stainless, or vice versa.

Metal | RECOMMENDED WIRE SIZES | ||||||
---|---|---|---|---|---|---|---|
Material Thickness | MIG Solid Wire | Gasless Flux-Core Wire | |||||
.024” | .030” | .035” | .045” | .030” | .035” | .045” | |
24 Gauge (.025) | |||||||
22 Gauge (.031) | |||||||
20 Gauge (.037) | |||||||
18 Gauge (.050) | |||||||
16 Gauge (.063) | |||||||
14 Gauge (.078) | |||||||
1/8” (.125) | |||||||
3/16” (.188) | |||||||
1/4” (.25) | |||||||
5/16” (.313) | |||||||
3/8” (.375) | |||||||
1/2” (.5) | |||||||
24 Gauge (.025) | |||||||
![]() *When welding materials that are thicker than 3/16” you may need to use Multipass or welding, or beveled joint design (depending on your machine).
|
Welding Wire Basics
WELDING WIRES | |
---|---|
Solid Carbon-Steel ER70S-6 |
|
Flux Cored/ Carbon-Steel E71TGX |
|
Aluminum ER5356 |
|
Stainless Steel ER308L |
|
Shielding Gas
Choosing The Right Shielding Gas
Co2 should be used with thick materials, but is too hot for thinner materials. Thin steel should be used with 75%Argon/25% Co2.
Aluminum should be used with Argon.
Stainless steels can be used with a triple-mix, or Helium+Argon+CO2.

Gun Techniques
Drag And Pull Gun Techniques
Drag/Pull= More penetration with a more narrow bead
Push= Less penetration with wider bead
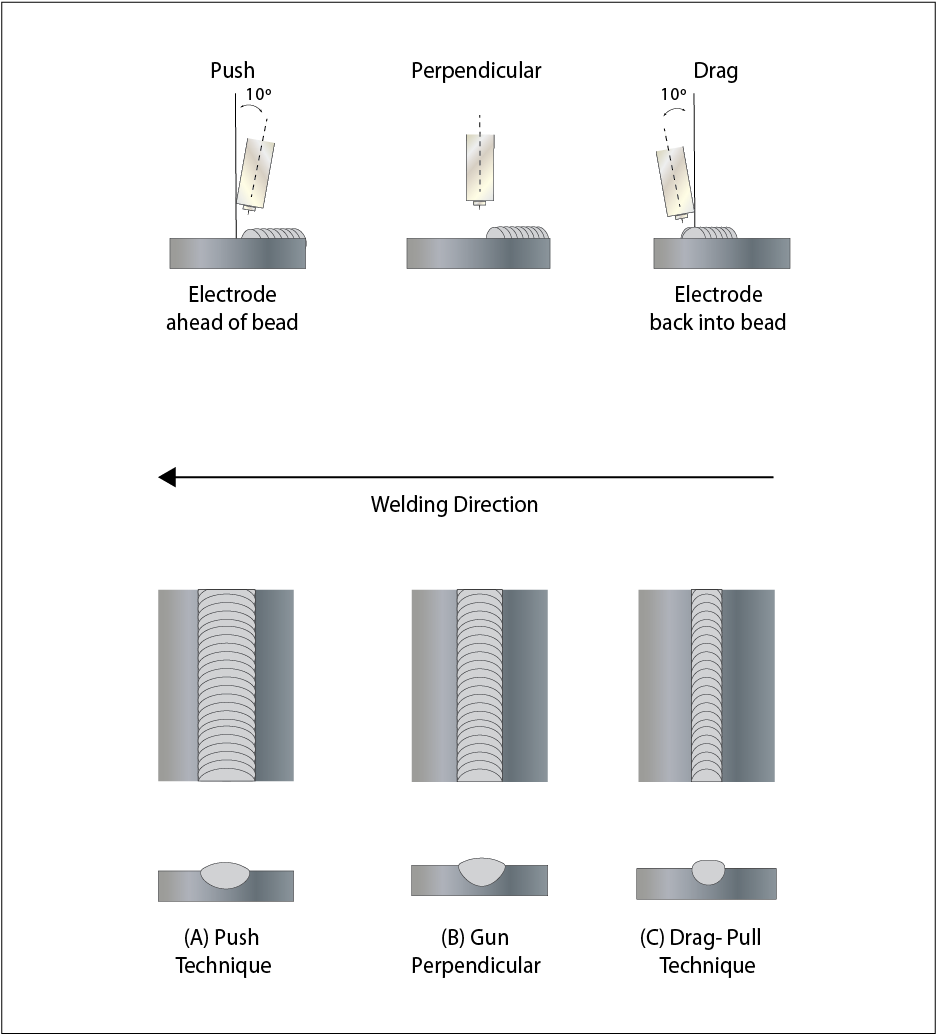
Fillet Welds
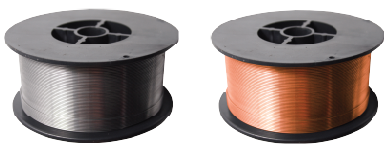
Fillet Weld Thickness
The Leg of your weld should be equal to the thickness of the materials you welded.
Aluminum MIG WELDING
Aluminum MIG Welding TIps
- It is highly recommended to use a spool gun when welding with aluminum. However, if you don’t have access to one, you can try using an extremely short gun.
- Keep your gun straight.
- Use Argon as your shielding gas
- Push gun away from you as you weld (Push gun technique)
- Feeder Problems? A possible solution to feeder problems is using a contact tip that is one size larger than your wire.
- ER403 wire can be used for most projects. ER4356 should be used when your weld needs to be stronger, or rigid.
- Always clean your aluminum before welding, using a stainless steel wire brush. This brush should only ever be used for cleaning aluminum wire to prevent contamination.
- Fill the crater at the end of the weld to avoid a crack. One way to do this is to dwell in the weld pool for a second at the end of the weld.
SElf-Shielded Flux cored WElding
Flux Cored Welding Tips
- Pull torch away from you as you weld (Pull gun technique)
- Store your wire in a dry place free of contaminates
- Use a chipping hammer and wire brush to remove slag layer after weld is complete
- You do not need shielding gas—Great for welding outdoors!
- You won’t be able to weld as thin of metals than would with normal MIG welding.
SPOOL GUNS
Why Use A Spool Gun?
Spool Guns are recommended to be used while welding aluminum. There are many benefits to using a spool gun on aluminum over your standard MIG torch, which include:
- Using a spool gun prevents you from contaminating aluminum with a gun that had been used with previous metals, ensuring the highest quality weld.
- Aluminum is more delicate of a metal. Spool guns have a far less distance to be fed through, which means less chances of the aluminum kinking.
- Aluminum needs to expand as it comes out of the contact tip. The diameter of a spool gun contact tip is much bigger than that of a MIG gun, giving the aluminum the room it needs.

Great Starter Machines

MIGWELD® 100
One of our great MIG welding starter machines is the MIGWELD® 100. The MIGWELD® 100 will easily connect to your existing 110v wall outlet and can be setup easily in minutes. Running on a standard 110v power cord and capable of holding up to an 11lb spool, you will be able to lay down a nice weld anywhere without gas! The MIGWELD® 100 also has easy, user friendly controls which allows you to setup your machine quicker, more easily, and accurately.
MIGWELD® 140
The MIGWELD 140 is the most versatile welder which will do aluminum with the optional spool gun in addition to all exotic metals. The MIGWELD 140 will easily connect to your existing 110v wall outlet and can be setup easily in minutes. Running on a standard 110v power cord and capable of holding up to an 11lb spool, you will be able to lay down a nice weld anywhere with or without gas! This makes the MIGWELD® 140 another great starter machine.

Intermediate Machines
MIGWELD® 200S
If you’ve practiced all the basics and are ready to dive into a more advanced machine , with more control, and the ability to weld more exotic metals , then the MIGWELD® 200S is great machine for you! This machine is very similiar to the MIGWELD® 140, with a little more power and little more options.

For more MIG welding technique information Check out these links
Longevity’s TIG Welding Video Library (Click Here)
BASICS OF SELF SHIELDED FLUX CORE METAL ARC WELDING

Scott shows off the skip welds using a LONGEVITY Migweld 100 - flux core mig welder. Technique is explainedThis is just one of our many welding videos in our library.
Longevity’s MIG Weld Calculator (Click Here)
No matter if you’re a beginner welder, or an industry pro every now-and- then everyone needs a little help with figuring out what settings to use while welding new materials. Instead ofwelding without any idea of what settings to use, try out our Welding Calculator. All you have to do is pick your process, type of metal, thickness of metal, and weld type then all your questions will be answered. Welding guides lines you’ll be recommended are; electrode diameter, polarity, torch cup orifice diameter, filler metal diameter, gas, gas flow rate, and welding speed.

Longevity’s FREEWELDINGFORUM.COM
MIG Welding Project Done By Forum User: ironheartram

Our Free Welding Forum is a great place for all welders to share knowledge they have gained no matter if they are a beginner welder, or an industry pro. All the questions you want answered could be done by just reaching out on our forum. If you’re looking for help, to help, want to check out some really cool projects, or just meet people that share your same passion for welding, Longevity’s Free Welding Forum is the perfect place to go!